
Maximizing efficiency, profitability,
& customer satisfaction
in every glass solution.
Bullan Packaging Center was founded by Charles Bullan nearly 30 years ago, and we have been committed to providing a superior packing solution in the repack and reselection industry ever since.
Trusted by leading glass manufacturers for years
We proudly continue to deliver reliable, high-quality solutions that meet and exceed industry standards.
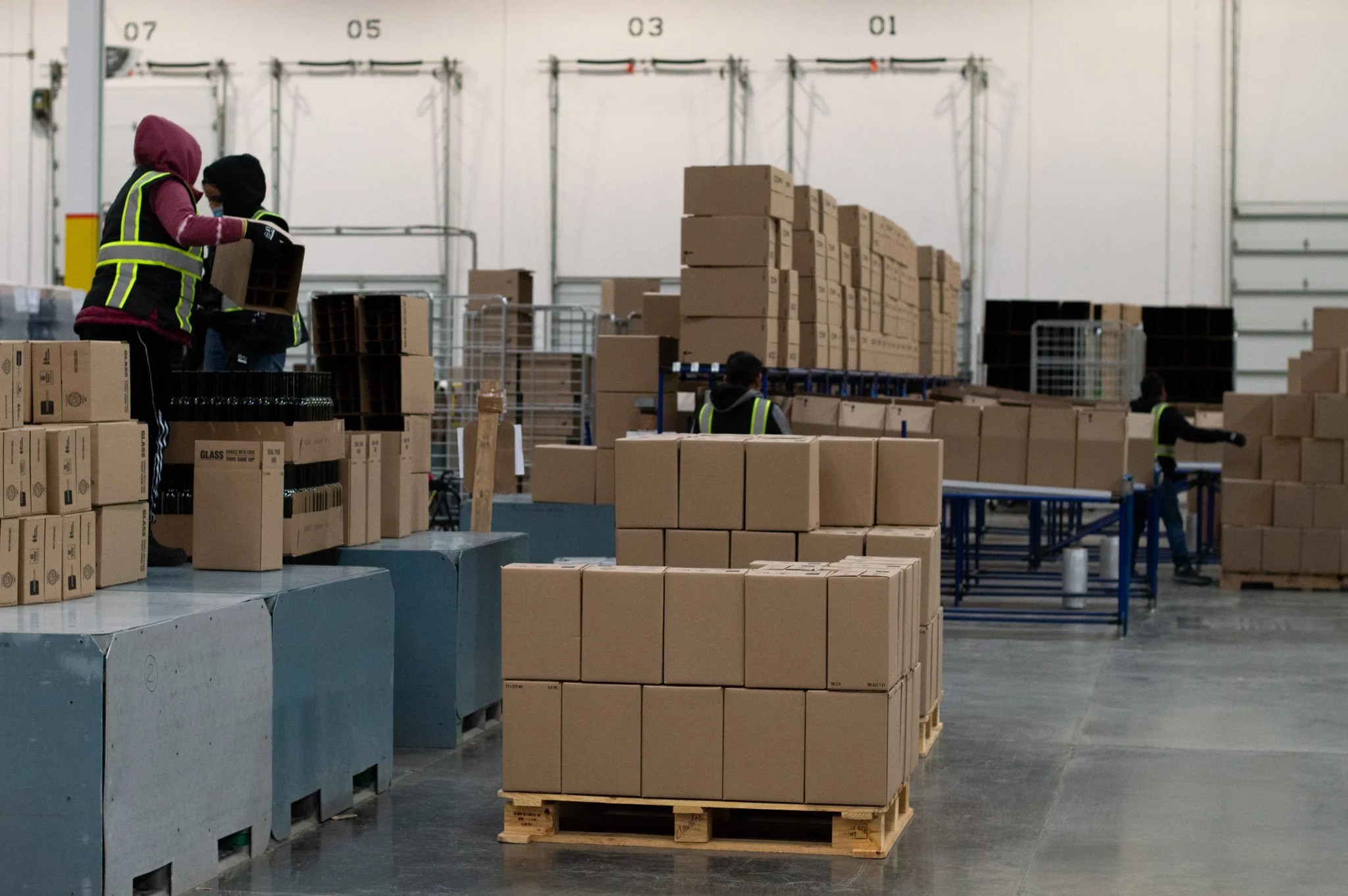
Comprehensive Glass Solutions
Repacking & Handling
Automated Equipment Repacks & Manual Repacks: Efficient repacking solutions for a variety of equipment.
Reselections & Cavity Culls: Ensuring precision and quality in product sorting.
Re-stacks: Expert reorganization for better storage or transport.
Labeling & Identification
Labeling/De-Labeling: Organizing and preparing products with precision.
Glass Recycling: Environmentally friendly recycling solutions.
Quality & Compliance
Audits: Comprehensive checks to meet your quality standards.
AQLS (Acceptable Quality Limit Standards): Maintaining the highest quality thresholds for your products.
4/3 Splits: Specialized quality control services tailored to your needs.
Storage & Warehousing
Storage/Warehousing: Secure and efficient storage options for your products.
Cleaning & Maintenance
Wipe Downs: Ensuring equipment and products are clean and ready.
Heat Tunnel Projects: Efficient handling and maintenance for heat-based operations.
Specialized Services
Mobile Team: We come to you, providing flexibility and convenience.
Clamping Services: Safe and effective handling of specialized equipment.
A Commitment to Quality
-
We prioritize expertise from the start. Every employee completes a 30-day training program that includes:
In-depth lessons on identifying defects in glass, cartons, partitions, and packaging.
A glass terminology handbook paired with hands-on defect samples for practical learning.
Rigorous testing to ensure knowledge and readiness.
-
To maintain our high standards, we continually evaluate employee performance:
Supervisors conduct daily quality checks using production check sheets.
These checks are conducted without the employee’s knowledge to ensure accurate and objective evaluations.
Feedback and retraining are provided as needed to maintain consistent quality.
-
Safety and accountability are integral to our operations:
All forklift drivers are certified and undergo regular checks.
Drivers inspect each pallet before shipment and complete a certification check sheet attached to every Bill of Lading, so you can be sure every driver is held accountable for the pallets they have loaded.
Certifications are prominently displayed to affirm our commitment to compliance and professionalism.
-
Our facility is equipped with cutting-edge tools to ensure precision and accuracy, including:
Light plate tables, out-of-round gauges, and black lights.
Over max T-dimension gauges, plug gauges, and calipers.
Glass cutting equipment and inside bore diameter gauges for detailed inspections.
-
Our quality assurance processes are guided by well-defined SOPs that:
Establish consistent, repeatable methods for inspections and reselections.
Cover common issues such as blow tube marks, plunger pulls, and more.
Ensure every product meets or exceeds industry standards before leaving our Fairfield, California based facility.
Our Promise To You
Dedicated Team
Customer-First Focus
Proactive Problem-Solving
Hassle-Free Resolutions
Guaranteed Confidence
Dedicated to excellence, our skilled staff works tirelessly to deliver superior workmanship and unparalleled customer service. In the rare event of a concern, we stand by our promise to make it right—whether through free rework or an on-site inspection by trained professionals.
Customer satisfaction is at the heart of everything we do. We prioritize your experience by ensuring our team follows strict Standard Operating Procedures to maintain consistency and quality. Our proactive approach means we address potential issues before they arise, saving you time and stress.
If we ever cause a missed shipment or downtime, we take full responsibility, covering costs as needed. With every project backed by a 100% guarantee, you can trust us to deliver with integrity and care.
Contact us.
Victoria Ramírez -
Victoria@qxcompany.com
Rony Mora -
Rony@qxcompany.com
Monique Martinez -
Monique@qxcompany.com
(707) 426-5000
2300 Cordelia Rd. Ste. B
Fairfield, CA 94534